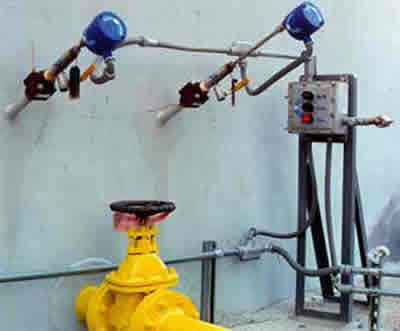
Storage tanks containing hydrocarbon feedstocks, intermediates and finished products will, over time, accumulate a water layer in the bottom of the tank (exceptions are water-soluble hydrocarbons such as alcohols and ethers). Standard industry practice is to periodically drain the water from storage tanks so that the water does not adversely impact specifications of the hydrocarbon.