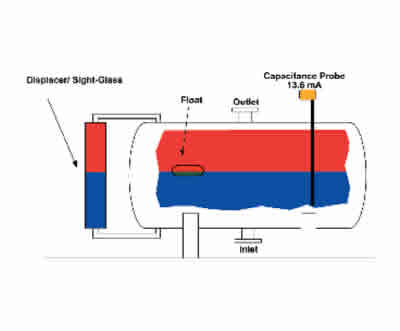
Free Water Knock-Outs, Desalters and Dehydrators are just some of the applications in the oil industry where it is necessary to separate water and oil. The density differences between water and oil causes water to drop to the bottom of a separation tank, and oil to rise to the top.