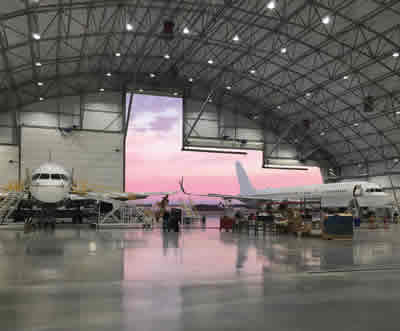
AAR MRO Services supports airline operators with everything from maintenance inspections and equipment upgrades to airframe painting and heavy maintenance for all major aircraft in service. The largest MRO operator of its type in the Americas, AAR recently opened the company’s largest facility, located at the Chicago Rockford International Airport.